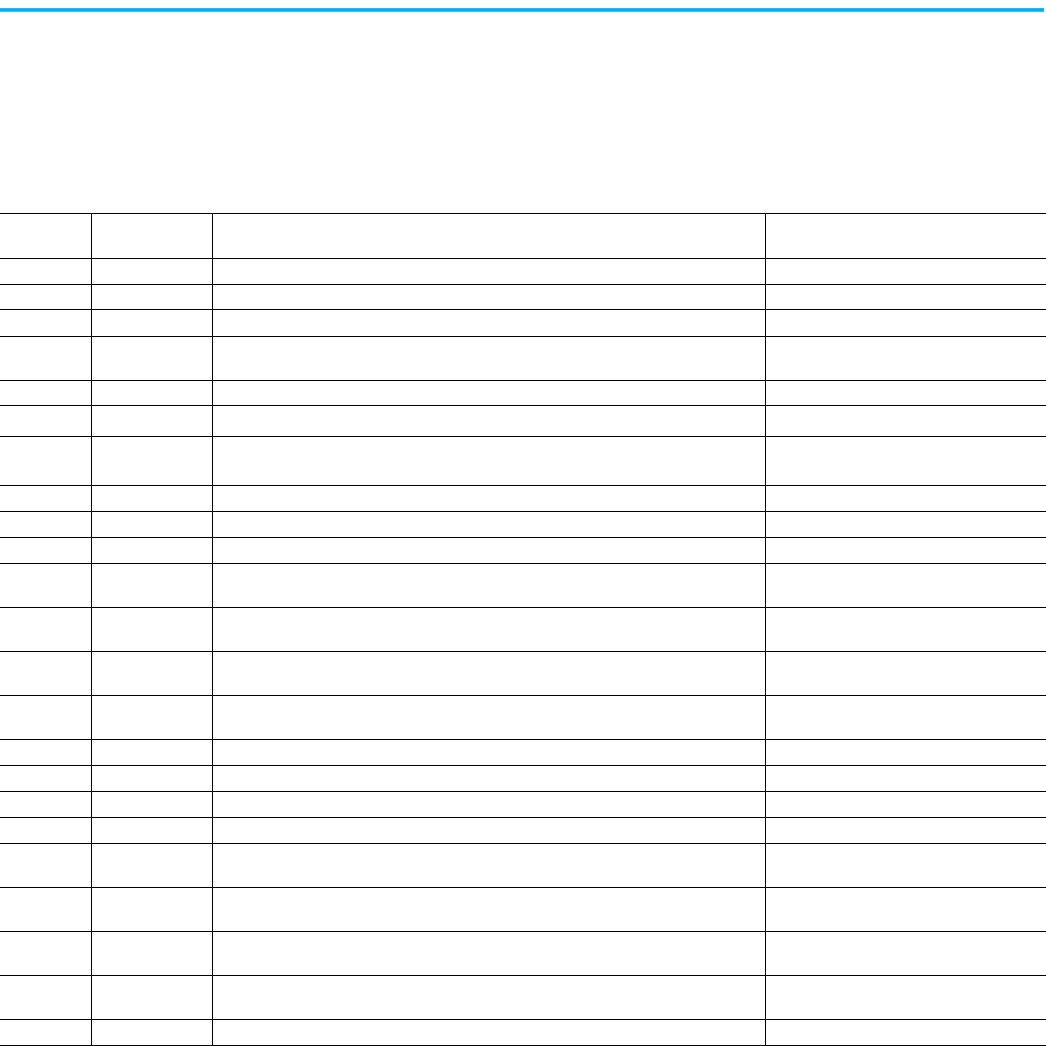
Rockwell Automation Publication 150-UM008I-EN-P - October 2020 89
Chapter 4 Programming
Basic Setup
The Basic Setup programming group provides a limited parameter set,
allowing quick startup with minimal adjustment. If you plan to implement
some of the advanced features (such as Dual Ramp or Preset Slow Speed),
select the Setup programming group. It provides the complete Basic Setup
parameter set and the advanced set.
Table 26 - Basic Setup Parameters
Parameter
No.
Parameter Name Description Value
14 SMC Option Displays the type of controller. This is factory set and not adjustable. Standard
15 Motor Connection Displays the motor type to which the device is being connected. Line or Delta
16 Line Voltage Displays the system line voltage to which the unit is connected.
17 Starting Mode
Lets you program the SMC Flex controller for the type of starting that best fits the
application.
Soft Start, Current Limit, Full Voltage, Linear
Speed
18 Ramp Time Sets the time period during which the controller will ramp the output voltage. 0…30 s
19
Initial Torque
(1)
Establishes and adjusts the initial reduced voltage output level for the voltage ramp. 0…90% of locked rotor torque
20
Current Limit
Level
(2)
The current limit level that is applied for the Ramp Time selected. 50…600% FLA
22 Kickstart Time A boost current is provided to the motor for the programmed time period. 0.0…2.0 s
23 Kickstart Level Adjusts the amount of current applied to the motor during kickstart. 0…90% of locked rotor torque
133 Stop Input Lets you select the operation of terminal 18, Stop Input. Coast, Stop Option
132 Option Input 1 Lets you select the operation of terminal 16, Option Input #1.
Disable, Coast, Stop Option, Fault, Fault NC,
Network
24 Option Input 2 Lets you select the operation of terminal 15, Option Input #2.
Disable, Slow Speed, Dual Ramp, Fault, Fault
NC, Network, Clear Fault
32 Stop Mode
Lets you program the SMC Flex controller for the type of stopping that best fits the
application.
Disable, Soft Stop, Linear Speed
33 Stop Time
Sets the time period during which the controller will ramp the voltage during a stopping
maneuver.
0.0…120 s
44 Overload Class Lets you select the Overload Trip Class. Disable, 10, 15, 20, 30
45 Service Factor Lets you program the service factor from the motor nameplate. 0.01…1.99
46 Motor FLC Lets you program the FLC from the motor nameplate. 1.0…2200
47 OL Reset Lets you select the type of overload reset. Auto, Manual
107 Aux1 Config
Lets you configure the operation of the contacts that is located at terminals 19 and 20.
Contact is provided as standard with the SMC Flex controller.
Normal, Up-to-speed, Fault, Alarm, Network
Control, External Bypass: (N.O.)
110 Aux2 Config
Lets you configure the operation of the contacts that is located at terminals 29 and 30.
Contact is provided as standard with the SMC Flex controller.
Normal, Up-to-speed, Fault, Alarm, Network
Control, External Bypass: (N.O.)
108 Aux3 Config
Lets you configure the operation of the contacts that is located at terminals 31 and 32.
Contact is provided as standard with the SMC Flex controller.
Normal, Up-to-speed, Fault, Alarm, Network
Control, External Bypass: (N.O.)
109 Aux4 Config
Lets you configure the operation of the contacts that is located at terminals 33 and 34.
Contact is provided as standard with the SMC Flex controller.
Normal, Up-to-speed, Fault, Alarm, Network
Control, External Bypass: (N.O.)
115 Parameter Mgmt Recall of factory default parameter values. Ready, Load Default
(1) Starting Mode must be programmed to Soft Start to obtain access to the Initial Torque parameter.
(2) Starting Mode must be programmed to Current Limit to obtain access to the Current Limit Level parameter.